
Showcase of STILFOLD Potential
Highly flexible, energy efficient and low investment process.
STILFOLD uses a unique recipe of art, design, mathematics, geometry and material material science powered by computational design software, atomisation and AI - enabling in essence Sustainable Origami Designs with less parts, weight and tools needed.
See below for some examples of our exciting development projects.
”STILFOLD has the potential to take a huge leap in reducing GHG emissions in the production phase. Low investment, energy use and waste reduction are some of the benefits. With unmatched reduction of parts and material saving we reach a CO2 reduction potential of 75% already today.”
Christian EngeneSustainability Expert at ReManufaktur

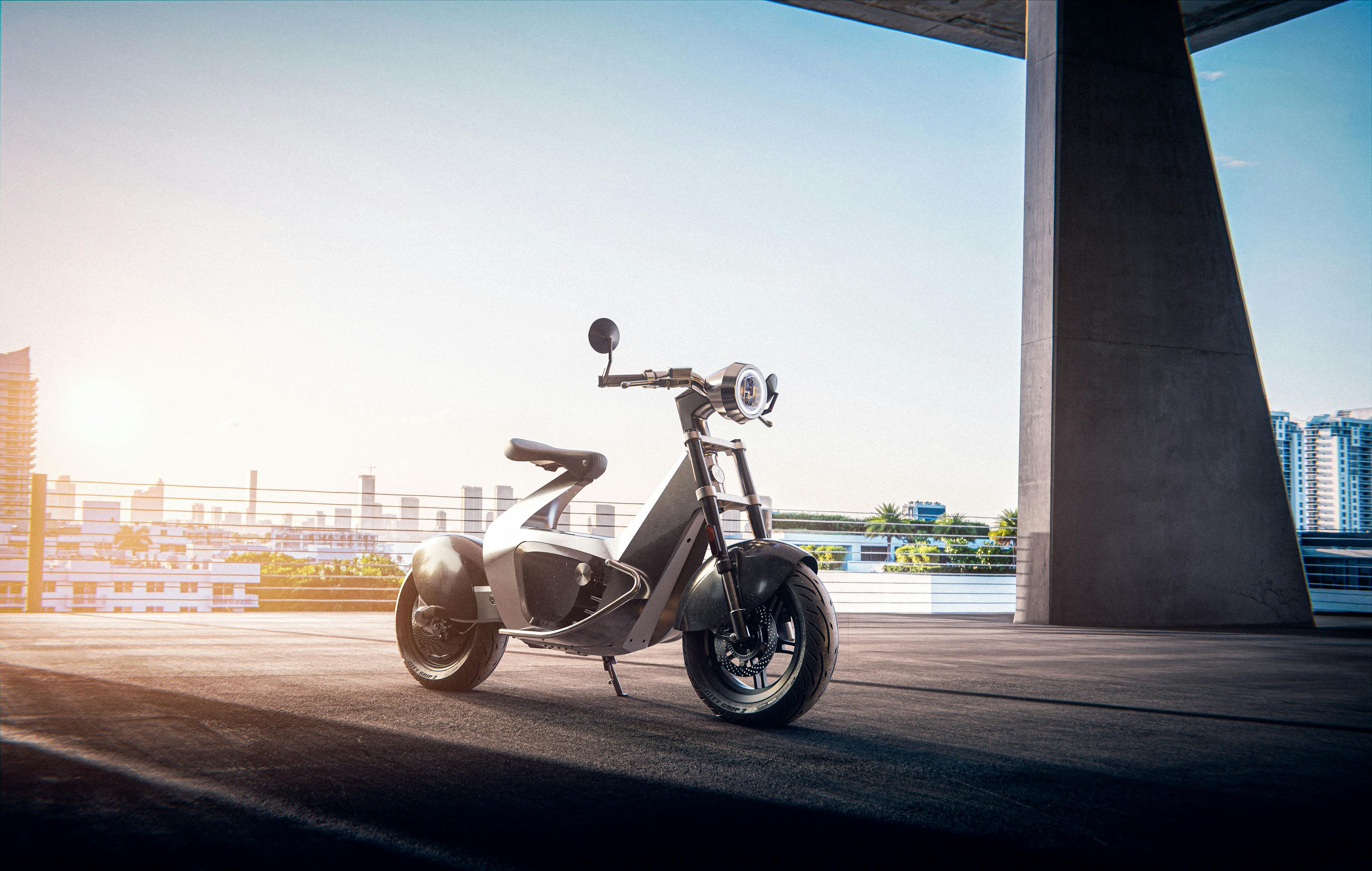
STILRIDE 1 is the ultimate light electric motorcycle for urban mobility. It combines cutting-edge design, technology, and sustainability to offer a smooth, fast, and eco-friendly ride.
We reduce the material usage by 50% compared to a market leading Chinese reference scooter. The process is also designed to dramatically lower the scrap rate of steel sheet pressing which in existing processes are creating up to 50% production scrap.
The carbon performance potential, CPP is estimated to 75% of CO2 eq reduction trough 50% material emission factor reduction and chassis weight reduction of 50%.
The CO2 eq reduction of a STILRIDE 1 chassis is estimated to 79 kg CO2 eq per produced unit compared to the competitor chassis. This is metal weight reduction only. Other components of the competitor chassis such as plastic covers and brackets are not included in this study.
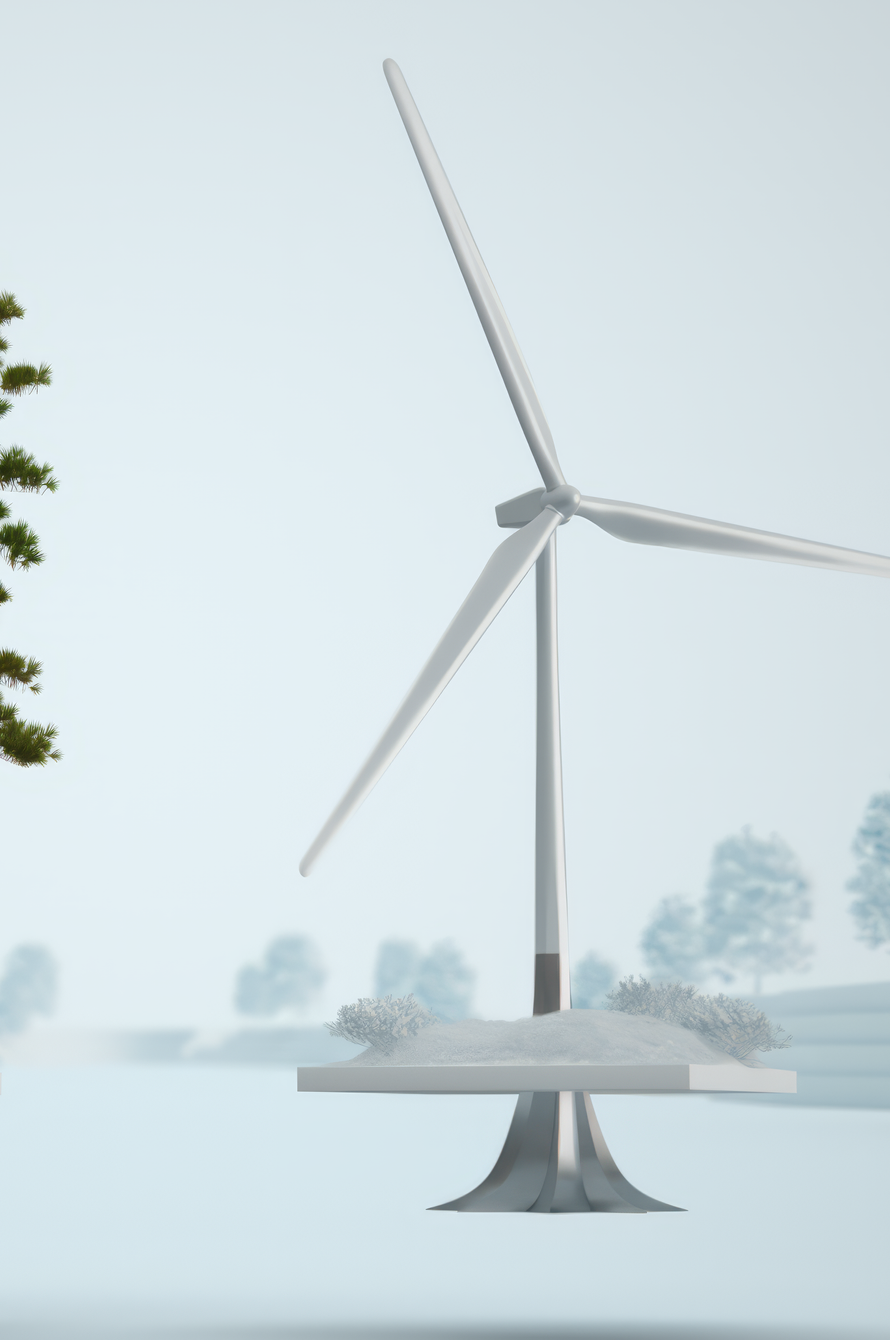
Using STILFOLD Technology for biomorphic inspired manufacturing of a wind turbine foundation enables a structure with optimal load path distribution and stiffness. This result in reduced material usage and outstanding sustainability compared with traditional solutions.
The Climate Performance Potential over the next 5 years is 8.8 megatonnes that equals 25% of annual total CO2 emissions for Sweden.
Christian Engene, Sustainable Design Strategist comments:
“The renewable energy transformation will require about 12,000 land-based wind farms to be built in the next five year period. STILFOLD enables a more sustainable way of manufacturing, completely removing the need for concrete. STILFOLD uses the latest low carbon steel manufacturing technology with the potential to reduce environmental impact by 80% from existing designs. The total Climate Performance Potential could save over 8 Megatonnes of CO2 in the next five year period of wind power expansion.”
Henrik Sieurin, Expert Engineer in steel (PhD from KTH Royal Institute of Technology focused on steel and material optimisation) comments:
"Using STILFOLD for bionic-inspired manufacturing of a wind power foundation enables a structure with optimal load-path distribution and stiffness. This results in reduced material usage and outstanding sustainability compared with traditional solutions."

Jonas Nyvang, CEO and Co-founder at STILRIDE comments:
“The foundation of an onshore wind turbine in the 7-8MW range is constructed using over 1000m3 of concrete and 150 tons of steel reinforcement. This creates a number of challenges: economical (costs are huge), logistical (it’s not easy to produce and transport such high quantities of materials, it needs 100 truck loads) and technical (it’s difficult to deploy such a high volume of concrete)."
“Our new design solution offers a cost-efficient and environmentally-friendly way of building the foundation of wind turbines, by reducing the concrete required to anchor wind turbines in place. It also eases the logistical burden of wind turbine construction by enabling modular construction: the STILFOLD beams can be transported individually and assembled on site.”

Stockholm’s Golden Bridge (“Guldbron”) is made out of steel and weighs 3,400 tons.
It was built in China and transported to Sweden in one piece, with a total carbon footprint of 15 million kilograms of CO2e (equal to almost 3000 transatlantic flights).
In comparison, STILRIDE’s industrial origami redesign would have:
• Reduced the carbon footprint by 60% (to 6 million kg CO2e)
• Cut transport emissions by 90%
• Used 20% less materials
• Preventing 9 million kilograms of CO2 from entering the atmosphere

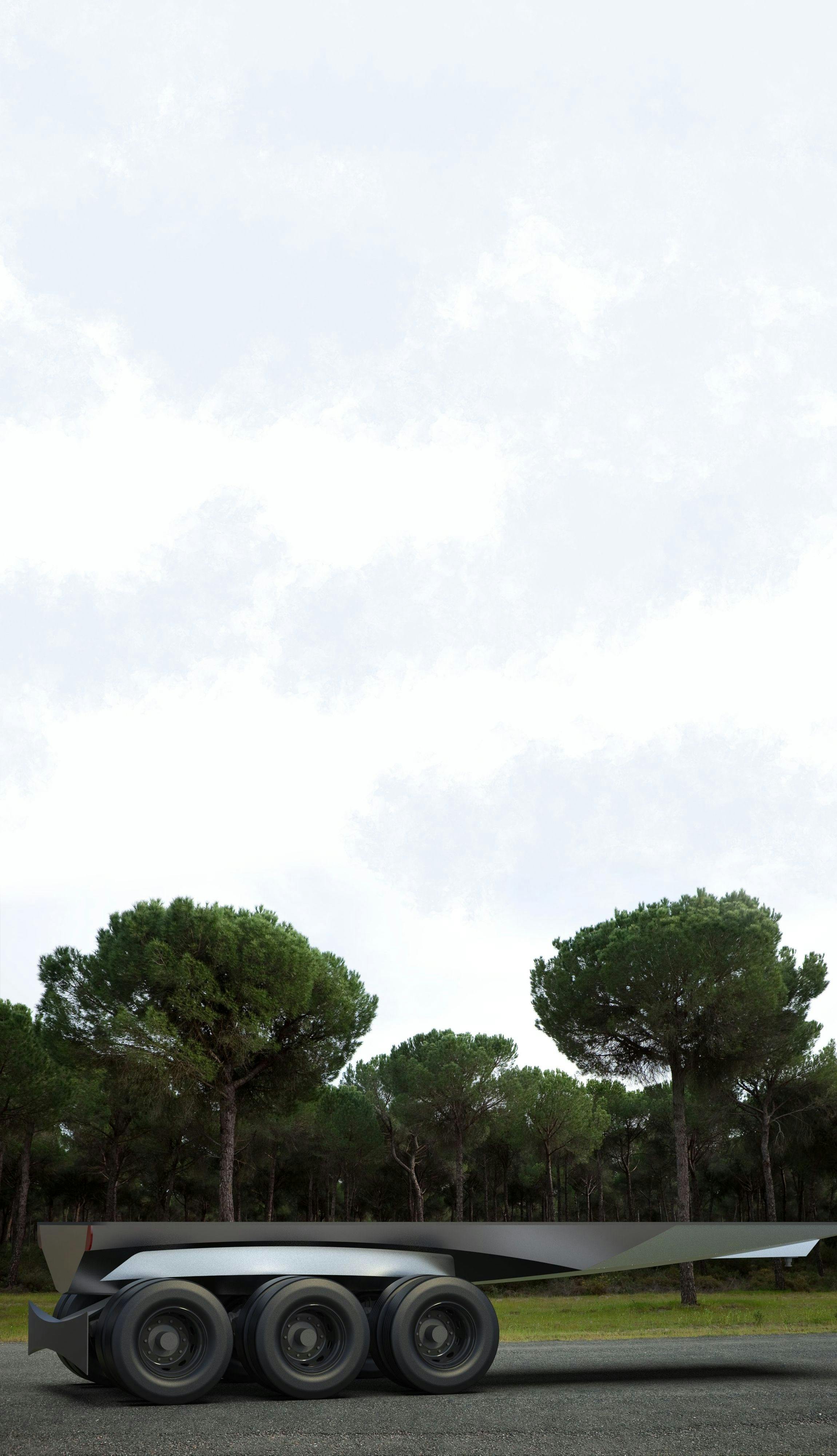
STILRIDE's trailer concept using the STILFOLD Technology for Greener Heavy Transports.
STILFOLD's exoskeletal design offers:
• Reduced weight with 30%
• 5% extra load capacity
• Enhanced aerodynamics & efficiency
• Reduced fuel consumption
RESULTS: 360,000 fewer transports & 12,000 tons CO2 saved yearly. A greener future for heavy transport!
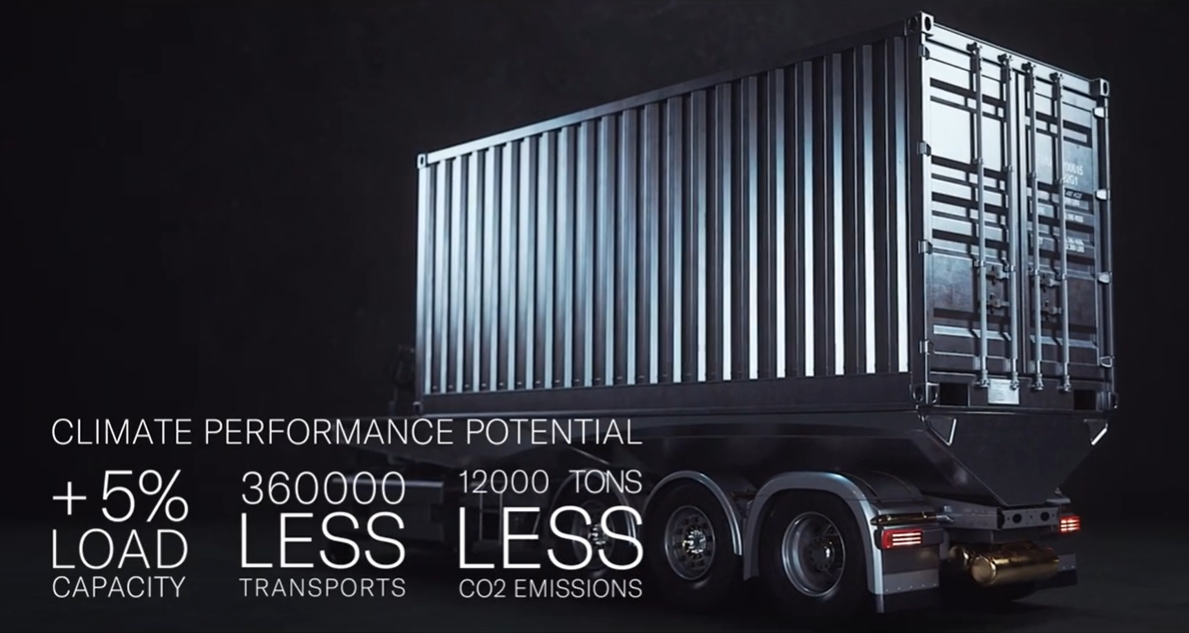
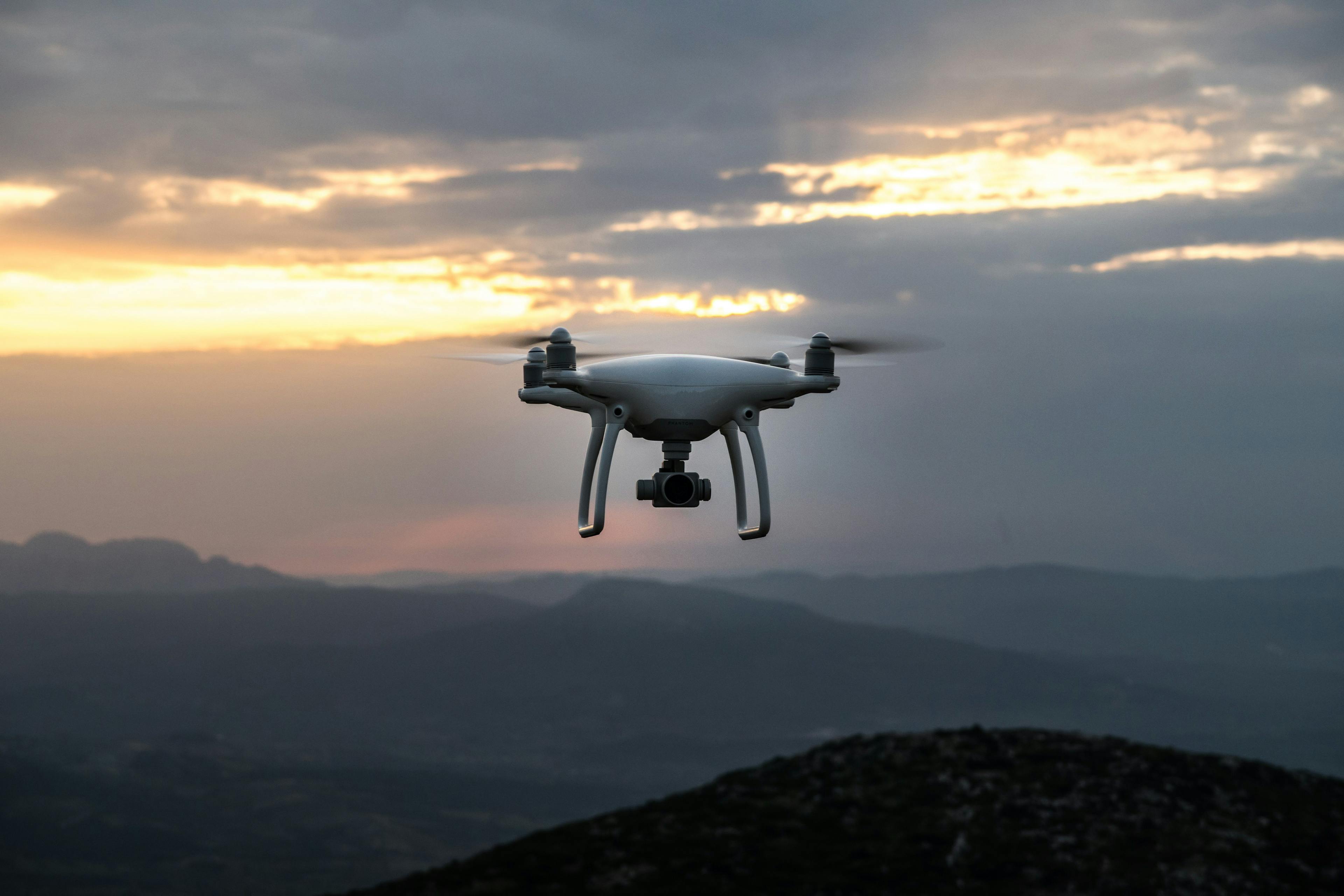
Through our collaboration with Kookiejar we aim to create a scalable and environmentally-friendly production solution for their vertiports.
The new vertiport foundation will be built by folding steel plates using STILFOLD’s origami-inspired manufacturing technology.
“Together with STILFOLD, we can find even more efficient ways to achieve our goals, build our vertiports, whilst streamlining our production processes and reducing our environmental impact.”, says Max Hoffman - Head of Strategic Projects at Kookiejar.

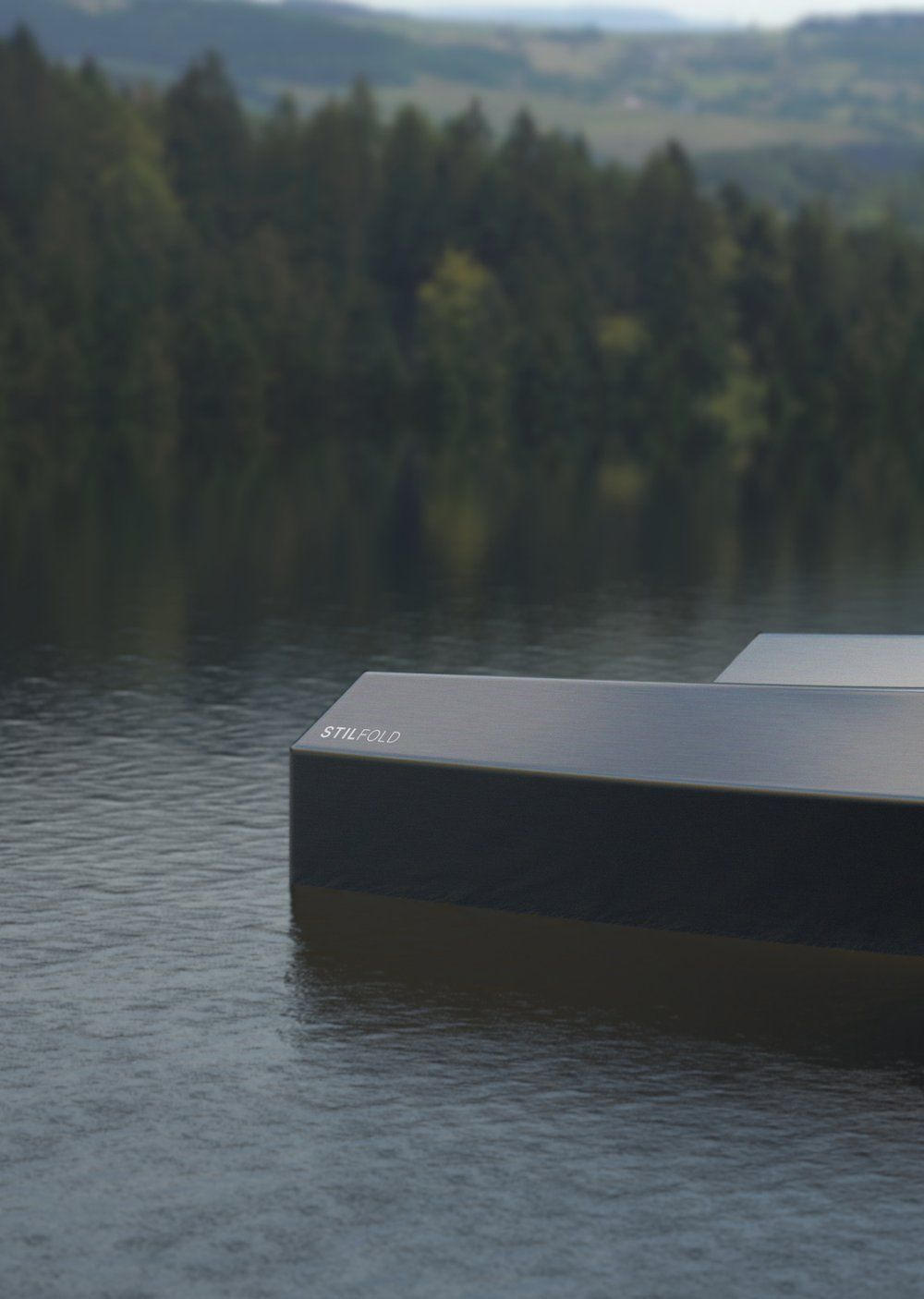
STILFOLD Technology's versatile applications transcend boundaries, from compact urban transportation and adaptable architecture to futuristic medical equipment, aerospace innovations, and shape-shifting fashion.
Its limitless potential across various sectors challenges conventional norms, fostering creativity and innovation.
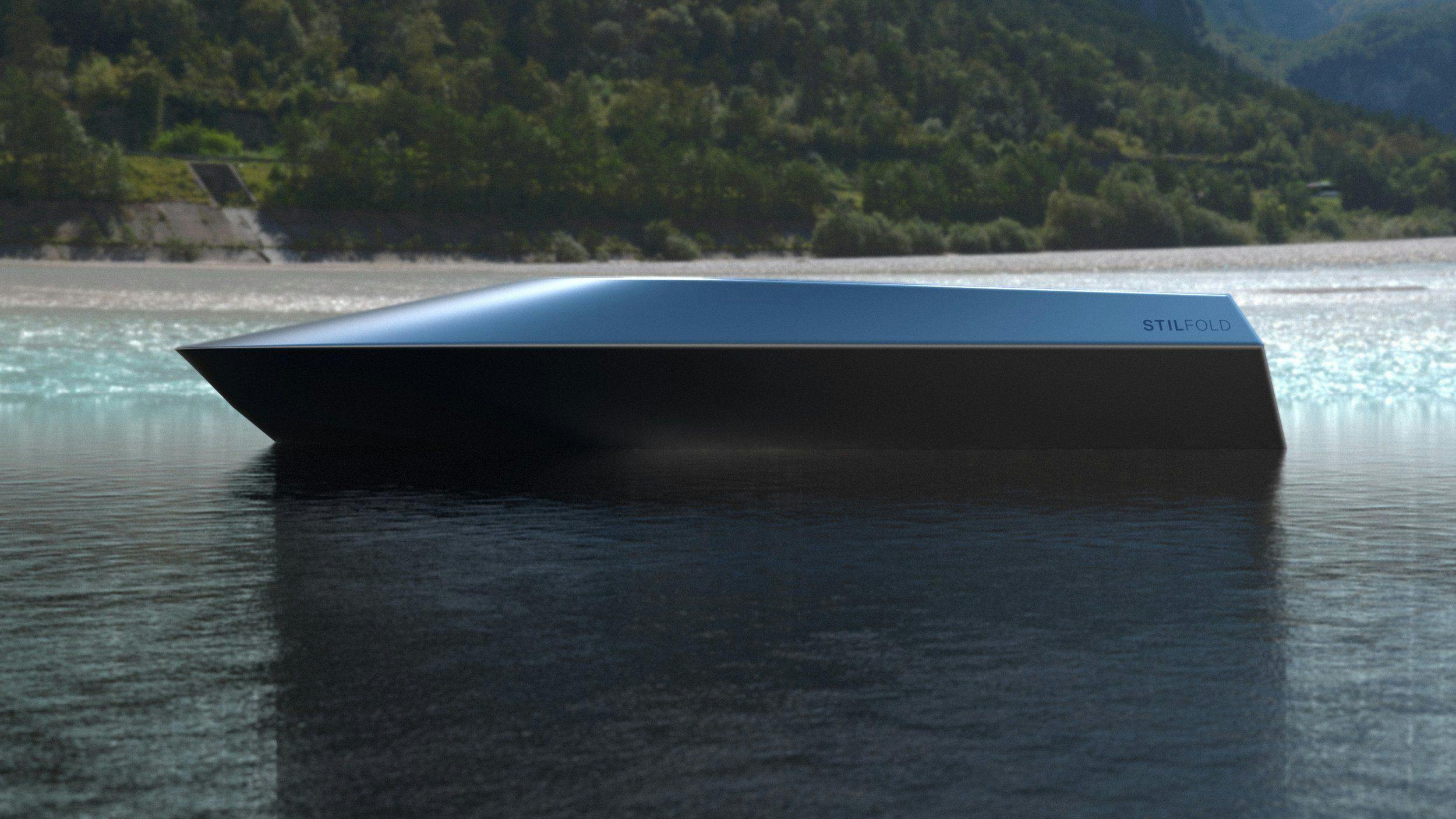